Production Processes
Innovative material processing technologies that optimise quality, time and costs
See all processesThe importance of experience
Know How
Novation Tech has a wealth of practical and theoretical knowledge which is also linked to the area where the company has grown. Thanks to this unique technological knowledge and skills, the company not only satisfies its clients’ needs but can also help them identify these needs, working together to choose the most suitable materials and technologies that will give the desired outcome, in terms of mechanics, aesthetics, time and costs.
Unique processes
Patents
6 patents, 20 different implementations: within these numbers lies one of the secrets to Novation Tech’s success. The company invests 7-8% of its turnover every year in research as developing processes and innovative production technologies is one of its main aims. Its R&D laboratory, located at the Montebelluna headquarters, works tirelessly to come up with more high-performance solutions, more efficient processes and more innovative technologies.
Production Processes
Autoclave moulding
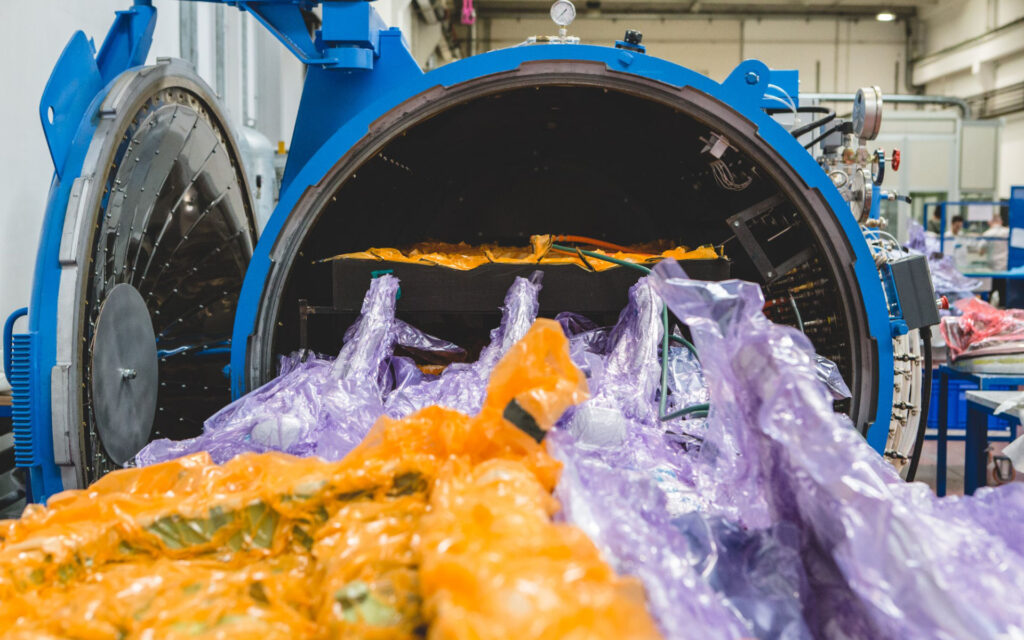
The autoclave process is the main procedure for producing high-quality composite components. Heat and pressure are applied uniformly to thermally cure the carbon fibre materials.
Novation Tech uses composite layups to combine prepreg materials with metal inserts, honeycomb materials and expanded materials.
Production Processes
Compression moulding

Compression moulding is a mechanical moulding process. The material to be moulded, if necessary preformed or pre-heated, is left inside a mould to polymerise (if it is a thermoset) or consolidate (if it is a thermoplastic). This process has low running costs and is ideal for large volumes.
Production Processes
RTM Moulding
Advanced RTM Moulding
Light RTM Moulding
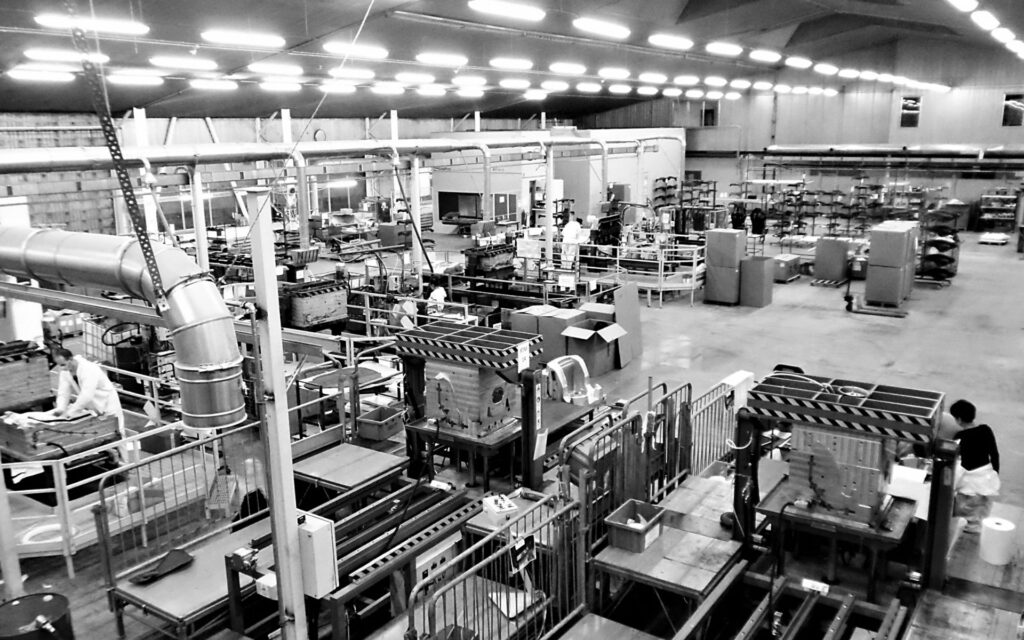
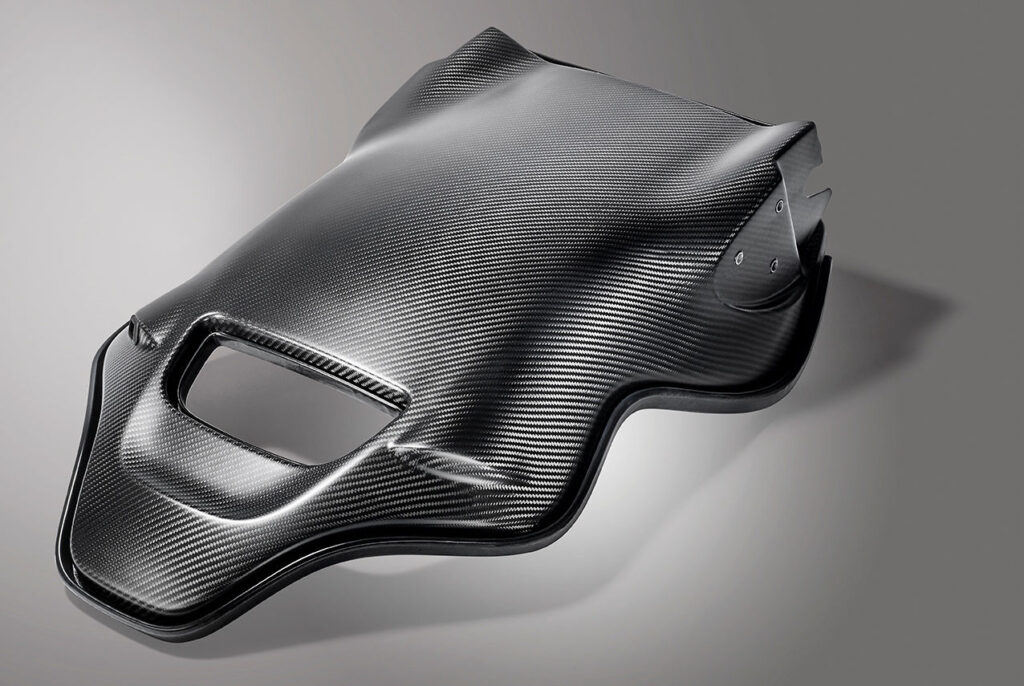
Advanced RTM Moulding
Resin Transfer Moulding (RTM) uses moulds made up of a matrix and punch. Resin under pressure is injected into the mould where the composite reinforcement material (carbon, glass) has already been placed. This technology is by far the best option in terms of costs and performance for manufacturing components in medium to high volumes and when close control of thickness and a high quality surface finish on both sides are needed.
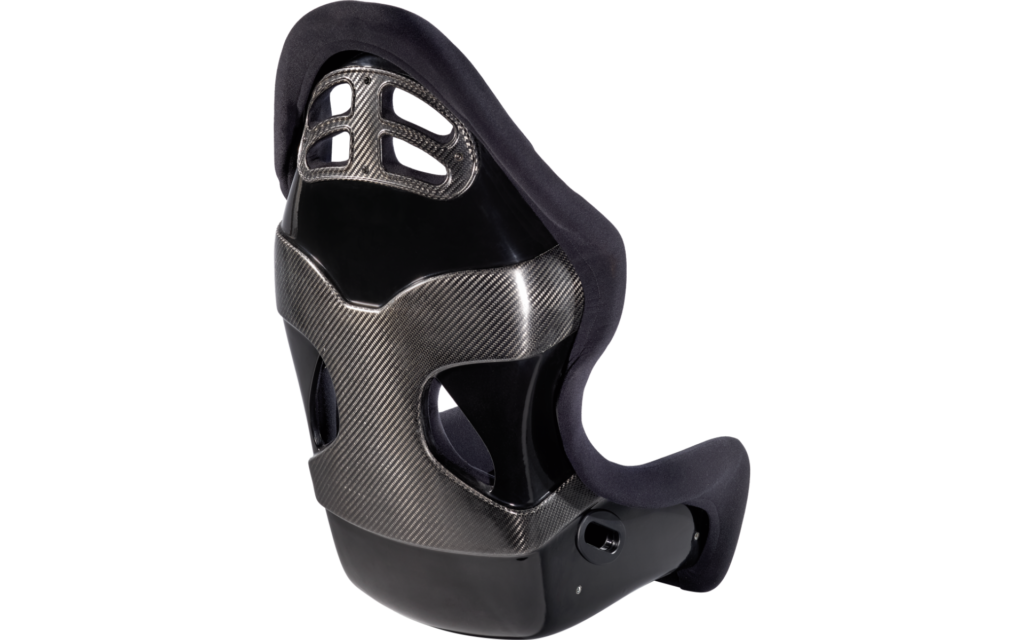
Light RTM Moulding
Light Resin Transfer Moulding, or Light RTM, is a process by which composite products are manufactured using a closed mould system. Resin is drawn into the cavity where the air has been vacuumed out. This technology is used to manufacture composite products with a fixed thickness, having good mechanical qualities, lower costs and reduced production times.
Production Processes
Finishing Operations
Water Jet Cutting Machine
CNC Milling Machine
Painting
Assembling
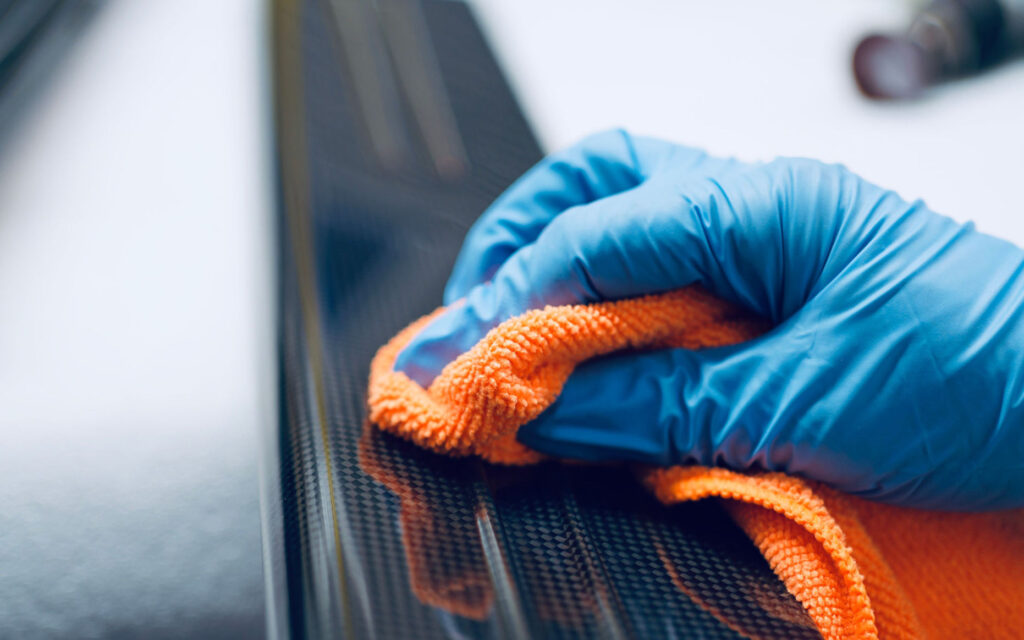
One of Novation Tech’s main assets is that it can handle every stage in a product’s creation, including the finishing operations. Novation Tech has also developed a series of processes to assemble sub-components (such as buttons, electronics, LCD screens), so it can deliver finished products to its client.

Water Jet Cutting Machine
The water jet cutter is well-known for the quality of the finish of the cut and its versatility. It is used for details and temples for eyewear.
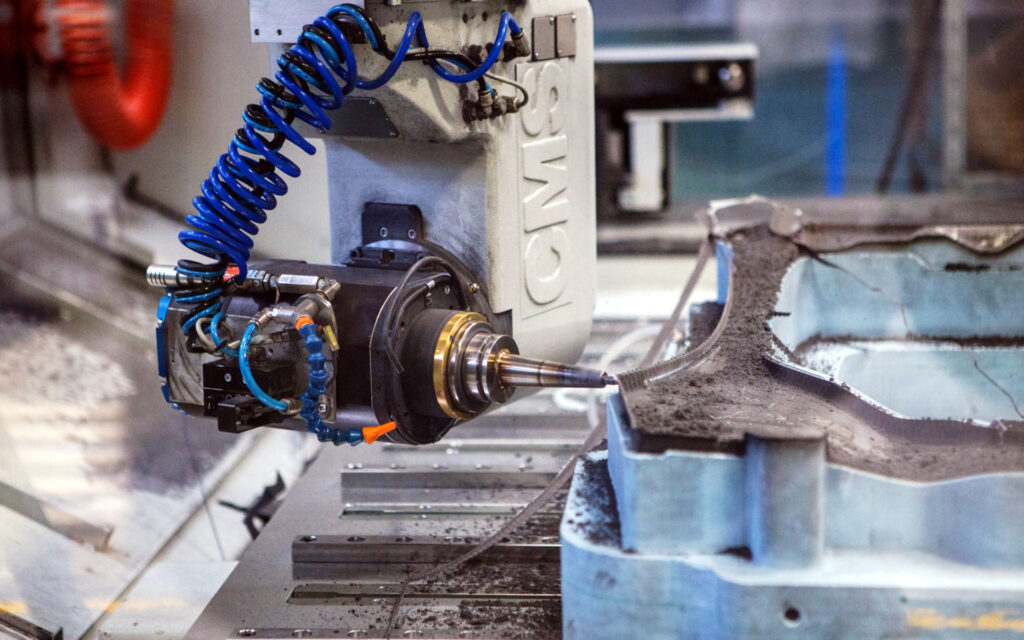
CNC Milling Machine
These are ideal work centres for carrying out complex, high-precision machining – the motions of the machine are controlled by numerical control, allowing it to perform many different processes such as milling, boring, drilling, threading etc…
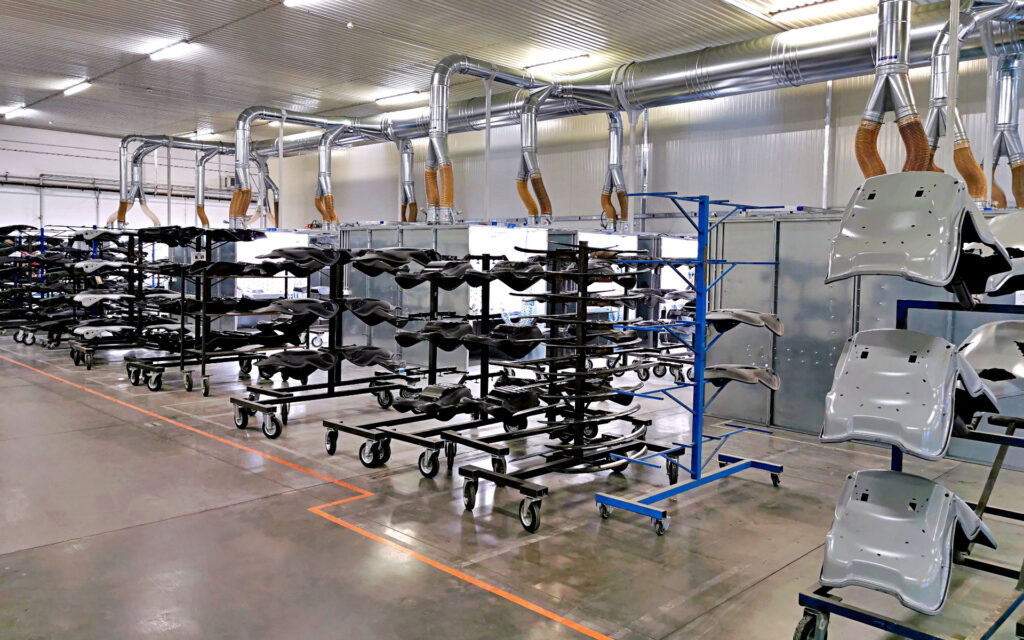
Painting
Novation Tech has three painting areas and a total of five heat treatment ovens. Highly aesthetic parts can have a glossy finish to create a bright effect, or a matte finish which gives the component a more modern and stronger appearance.
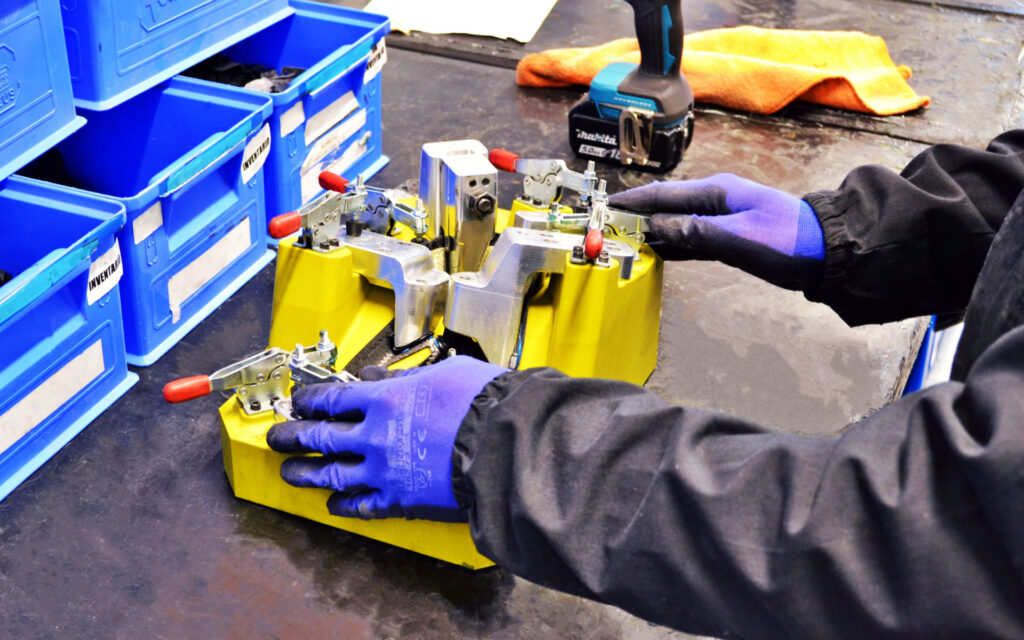
Assembling
Novation Tech assembles its components, ensuring products of the highest quality standards.
Production Processes
3D Printing
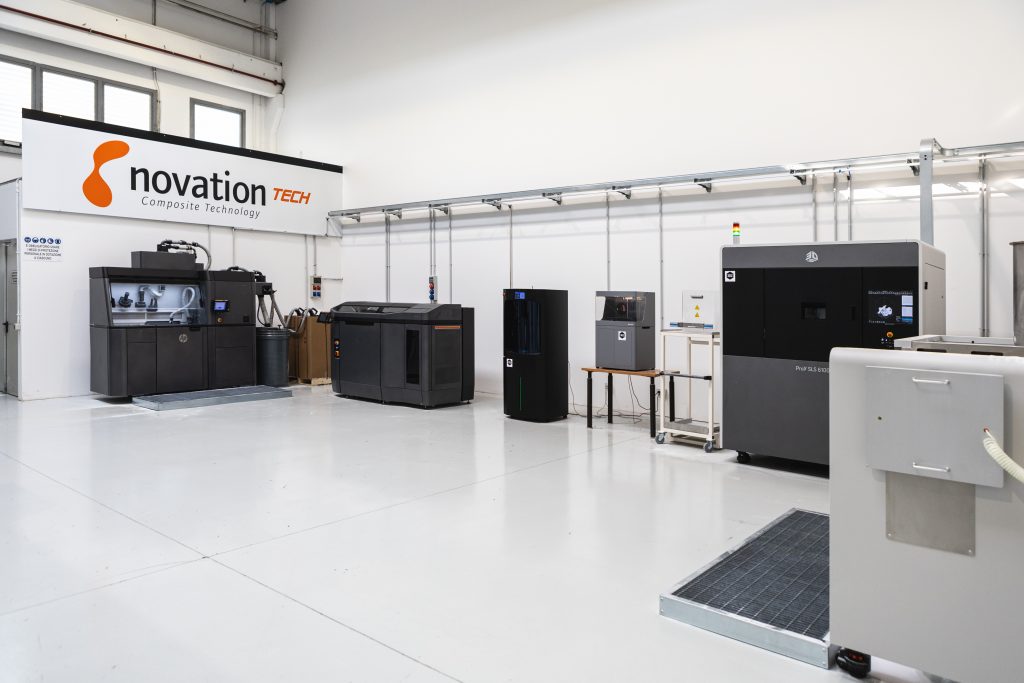
Novation Tech has a totally integrated 3D printing department with four different printers to create components in different materials. This state-of-the-art technological hub is one of its kind in the Veneto region and managed by a team of dedicated engineers.